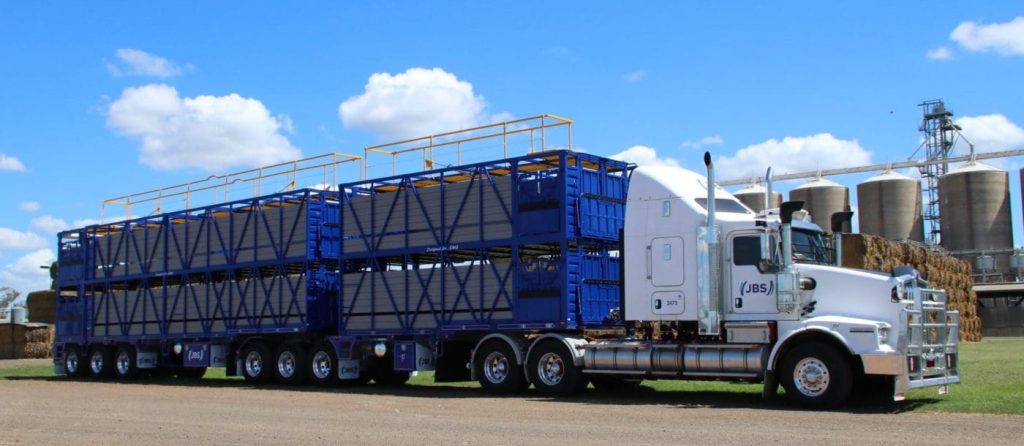
JBS Carriers B-Double at Beef City feedlot near Toowoomba
THE nation’s largest beef processor and lotfeeder, JBS Australia operates a large integrated livestock and freight haulage business designed mostly for internal use.
While this type of integration is rare in the Australian meat processing industry, parent company JBS operates a vast trucking fleet called Transportadora in its South American operations, numbering about 1100 trucks – the largest stock transporter in Brazil, and possibly the world. The JBS US division also runs a large trucking fleet.
JBS’s Australian livestock transport division numbering 18 Kenworth prime movers is part of a much larger JBS Carriers business, with a further 30 trucks hauling everything from refrigerated trailers carrying boxed meat to cold storage facilities, plus flatbeds, tankers and tippers hauling by-products like hides, tallow and other commodities from JBS plants in Queensland, NSW and Victoria. The total JBS Carriers fleet numbers 48 trucks.
All of the company’s stock transport work is cattle related – not lamb or pork.
Overseeing the business is Richard Horsham, general manager, JBS Carriers and Fleet, based out of Dinmore head office.
More livestock transport trucks will join the JBS Australian business this year, because of internal demand pressures, and some recent success with recruitment of drivers.
JBS Carriers appeared on the 2013 version of Beef Central’s Top 25 Transporters list, at that time in position 11, operating 20 prime movers with capacity for 69 decks. The company sits a little lower on this year’s list, due to growth among some other transport operators.
The JBS Australian transport business was established in 2010, three years after the company bought the former Australia Meat Holdings processing business, then owned by Swift & Co.
JBS Australia’s sheer size and vertical integration into lotfeeding, with feeding capacity above 130,000 head, always presented opportunities for the company in the transport sector, with the attraction of consistent, regular livestock freight run schedules.
Most of the company’s stock transport fleet runs B-doubles (three decks equivalent), but some roadtrains (six decks) are also used. The business maintains more trailers than required for the number of trucks to allow for servicing, different combinations and to support external tow partners.
The great majority of grain-finished cattle leaving JBS’s six feedyards (Beef City and Mungindi in Queensland, plus Prime City, Caroona, Riverina and Yambinya in NSW) are delivered to company-owned processing plants by JBS Carriers.
In addition, the business does some delivery of feeder cattle to the feedlots, from livestock suppliers’ properties, together with some direct-to-works and via-saleyards delivery of grassfed slaughter cattle to plants.
Vendors selling cattle to JBS are under no obligation to use the JBS Carriers business as part of the cattle sale process, and in fact many make their own arrangements. However at certain times, it makes logistical sense when JBS cattle buyers are putting lines of feeder cattle together.
“That ad hoc work is not necessarily a consistent part of our transport work, but we still do a fair bit of it,” Richard Horsham said.
In some cases, JBS chilled boxed beef heading to a port for export might have been on a JBS Carriers truck three times during the production cycle: once as a feeder animal to the feedlot, again from feedlot to processing plant, and lastly as boxed meat in a refrigerated container heading to port.
“On top of that, the tallow, hides and meat-meal from those cattle are transported for rendering or export in bulk or liquids form by JBS Carriers,” Richard said.
Security, reliability
So what advantage does financing and maintaining an internal stock transport fleet offer a business like JBS?
“It’s about security,” Richard said. “We know the trucks are there when we need them.”
“It’s also about flexibility, which is linked to the regular commitment to jobs. We’re here to service JBS, so we never have the conflict of having to prioritise one customer over another.”
“A good example is the feedlot business, for stock heading to the processing plants. The business is fairly routine, and we know well in advance about likely delivery numbers. There’s still fluctuation in numbers, but it’s a great arrangement for the feedlot staff, because they never have to think about organising transport for consignments, because we always have trucks available for them,” he said.
“On those odd occasions when the feedlot gives us an order and JBS Carriers does not have the trucks available, then we organise a sub-contractor.”
“But in reality they get this flexibility and security, where we basically never fail – because our focus is on the JBS business.”
The main base and maintenance facility for the JBS Carriers fleet is at the company’s Beef City feedlot near Toowoomba, but all feedlots have facilities for vehicles and staff.
Safety innovation award
JBS won a 2023 WorkSafe Queensland safety design award for its double-deck livestock trailers fitted with a pneumatically-operated handrail system, similar to other operational systems on tanker trailers (see yellow rails in the image above).
The concept was developed following extensive consultation with livestock drivers and trailer manufacturer, Rytrans.
We’ll circle back to discuss the system in an upcoming article on stock trailer design innovations, as part of this feature. Click the link below to view a short video on the award.
Booking inquiries: 0457 948 919
HAVE YOUR SAY